Sensor vs. Sensorless BLDC Motors
A Comparative Analysis
Sept 19, 23
Keshank Parmar
12 Minutes Read
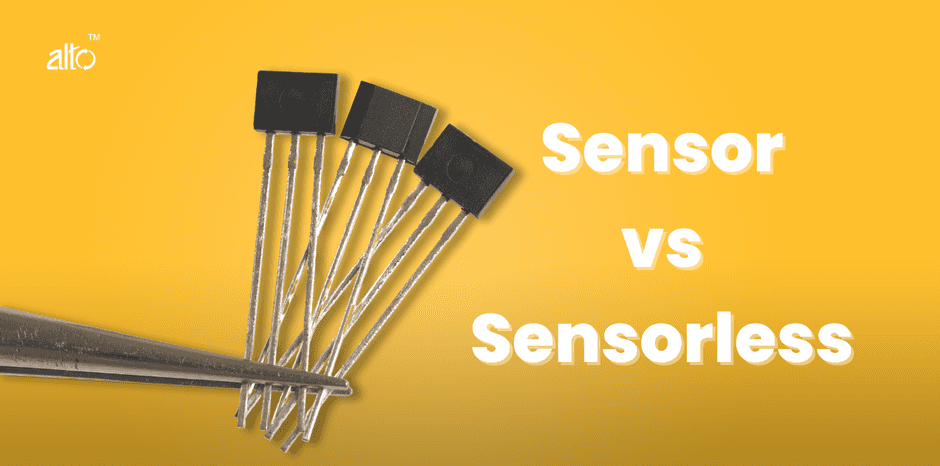
Introduction
Brushless Direct Current (BLDC) motors have grown in popularity due to their efficiency, longevity, and reduced noise compared to traditional brushed motors. One of the primary distinctions among BLDC motors is whether they are "sensored" or "sensorless." This blog post aims to shed light on the differences, advantages, and disadvantages of each type.
What is a BLDC Motor?
Before diving into the specifics of sensored and sensorless BLDC motors, let's briefly cover what a BLDC motor is. A BLDC motor is a type of electric motor that utilizes electronic commutation instead of mechanical brushes to transfer current. The lack of brushes results in reduced friction, heat generation, and wear, which in turn leads to increased efficiency and lifespan.
Sensored BLDC Motors
Definition
Sensored BLDC motors have built-in sensors, usually Hall effect sensors, that provide feedback on the rotor's position to the controller. This feedback allows the controller to precisely determine when to energize the next phase of the motor, ensuring smooth and efficient operation.
Advantages
1. Precision Control
The feedback provided by the sensors allows for precise control over the motor's speed and torque.
2. Smooth Low-Speed Operation
Sensored motors tend to operate more smoothly at low speeds because the controller always knows the rotor's position.
3. Reliable Starting
With positional feedback, the motor can reliably start under various load conditions.
Disadvantages
1. Cost
The inclusion of sensors increases the motor's cost.
2. Complexity
More wiring and a more complex control strategy are required.
3. Reduced Reliability
The presence of sensors introduces additional potential failure points.
Sensorless BLDC Motors
Definition
As the name implies, sensorless BLDC motors operate without any position sensors. Instead, they infer the rotor's position from the voltage and current measurements in the motor windings. This method, called back EMF detection, is used to determine when to switch the motor phases.
Advantages
1. Simplicity
No need for additional sensors simplifies the motor's design.
2. Cost-Effective
Generally, sensorless motors are cheaper due to the absence of sensors.
3. Higher Reliability
Fewer components mean fewer potential points of failure.
Disadvantages
1. Challenging Low-Speed Operation
Without direct feedback, sensorless motors might experience challenges during low-speed operation or starting under certain conditions.
2. Complex Control Algorithms
While the motor itself might be simpler, the control algorithms required for sensorless operation can be more complex.
Which One to Choose?
The choice between sensored and sensorless BLDC motors largely depends on the application:
For applications requiring precision control, especially at low speeds:
Sensored motors are typically the preferred choice.
For cost-sensitive or reliability-critical applications:
Sensorless motors might be more suitable.
In many cases, the decision will also be influenced by the experience and comfort level of the engineering team with the control strategies for each type of motor.
Conclusion
Both sensored and sensorless BLDC motors offer unique advantages and disadvantages. By understanding the needs of your specific application and weighing the pros and cons of each type, you can make an informed decision that best suits your requirements. As technology continues to evolve, we can expect further innovations in both categories, making BLDC motors even more versatile and efficient in the future.